When it comes to ensuring the safety, quality, and functionality of electrical and electronic equipment (EEE), regular inspections are crucial. EEE inspection Whether you’re a manufacturer, importer, or distributor of electrical products, adhering to inspection standards can help you maintain compliance, safeguard your business, and protect consumers. This guide breaks down the essential aspects of EEE inspection, including the standards you should follow, the steps involved in the inspection process, and the key benefits of regular inspections.
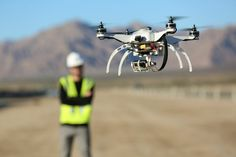
What is EEE Inspection?
EEE inspection refers to the systematic process of examining electrical and electronic equipment to verify that it meets established safety, performance, and regulatory standards. This inspection process is critical for ensuring that products are safe for use, are energy-efficient, and comply with national and international regulations.
These inspections are performed at different stages of a product’s life cycle, from design and manufacturing to post-market surveillance. The goal is to identify any potential risks or issues that could compromise the safety or performance of the product.
Key Standards for EEE Inspection
There are various international and regional standards that govern EEE inspections. Compliance with these standards ensures that products meet safety and quality requirements. Here are some of the most commonly recognized standards:
- IEC (International Electrotechnical Commission) Standards
The IEC is a global organization that develops international standards for electrical and electronic technologies. Key IEC standards for EEE include:- IEC 60335-1: Safety of household and similar electrical appliances.
- IEC 60950-1: Safety of information technology equipment.
- IEC 61000-4: Electromagnetic compatibility (EMC) standards.
- UL (Underwriters Laboratories)
UL is a safety certification organization that establishes standards for electrical equipment and ensures products are safe for use in various environments. UL standards cover everything from product construction to testing for electrical shock hazards. - RoHS (Restriction of Hazardous Substances Directive)
RoHS sets limits on hazardous substances in electrical and electronic equipment, such as lead, mercury, and cadmium, to promote environmental protection. - CE Marking
In the European Union, the CE mark is required for products sold in the region. It signifies that the product complies with all applicable European Union regulations regarding safety, health, and environmental protection. - ISO Standards
The International Organization for Standardization (ISO) provides standards for quality management, product safety, and environmental impact, such as ISO 9001 and ISO 14001.
Steps Involved in the EEE Inspection Process
EEE inspection typically involves several steps to ensure compliance with relevant standards. Here’s an overview of the key phases:
- Pre-Inspection Preparation
Before the actual inspection, businesses must gather all necessary documents, including product specifications, safety certifications, and test reports. The inspection team should also familiarize themselves with the relevant standards and regulations that apply to the specific product. - Visual Inspection
The first step in the inspection process is a thorough visual check. Inspectors will assess the physical condition of the equipment, looking for any obvious defects such as damaged cables, exposed wiring, or faulty components. - Electrical Testing
Electrical tests are performed to verify that the equipment operates within safe limits. This includes checking for proper grounding, voltage levels, insulation resistance, and the functionality of safety features like fuses and circuit breakers. - Performance Testing
Performance testing ensures that the equipment meets the required operational standards. Inspectors will test the product under various conditions, such as load testing and endurance tests, to confirm that it performs as expected. - Compliance with Regulatory Requirements
The equipment is assessed for compliance with national and international standards, such as those set by the IEC, UL, or CE. This may include checking labeling, documentation, and conformity to safety directives like RoHS. - Post-Inspection Documentation and Reporting
After the inspection, a detailed report is compiled, summarizing the findings. The report may include recommendations for addressing any issues discovered during the inspection. The product may be approved, rejected, or require modifications.
Benefits of EEE Inspection
Regular inspections of electrical and electronic equipment offer several advantages:
- Safety and Risk Reduction
Inspections help identify potential hazards such as electrical faults, short circuits, or fire risks before the product reaches the market. This ensures the safety of consumers and reduces the likelihood of product recalls or legal issues. - Regulatory Compliance
Adhering to inspection standards ensures that your products comply with the necessary regulations in the markets where they are sold. This minimizes the risk of penalties, fines, or loss of certification. - Quality Assurance
Regular inspections help maintain high product quality by identifying defects early in the process. This can lead to increased customer satisfaction and reduced returns or complaints. - Environmental Protection
Compliance with standards like RoHS helps minimize the environmental impact of EEE by reducing the use of hazardous substances in manufacturing processes and encouraging recycling. - Market Access and Brand Reputation
Products that pass EEE inspections are more likely to gain approval for sale in international markets. A product with a recognized safety certification also boosts consumer confidence and strengthens your brand’s reputation. - Cost Savings
Identifying issues early in the manufacturing process or during pre-market testing can save businesses from costly product recalls, lawsuits, or reputational damage. By catching problems early, companies can avoid expensive fixes later on.
Conclusion
EEE inspections are an essential part of the product development process, helping ensure the safety, quality, and compliance of electrical and electronic equipment. By following relevant standards and implementing a thorough inspection process, businesses can protect their products, customers, and reputation. Regular inspections not only reduce risks and costs but also provide valuable opportunities for quality improvement, leading to better-performing and safer products.
4o mini